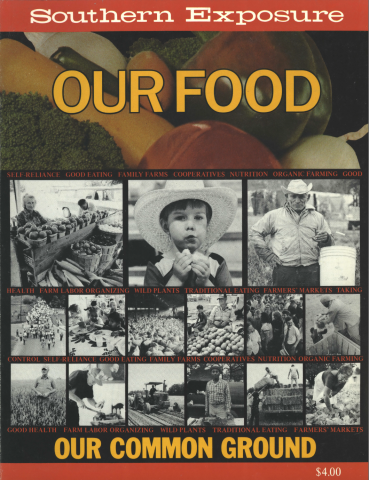
This article originally appeared in Southern Exposure Vol. 11 No. 6, "Our Food." Find more from that issue here.
The premiere agribusiness of the South is not cotton or tobacco, peanuts or soybeans, but the two-footed feathered creatures that go into Southern Fried. The Midwest can still lay claim to corn, wheat, and hogs — but the nation’s chicken-basket is in the South. At least 88 percent of the nation’s broilers — young chickens raised for meat — are born, raised, slaughtered, and processed here.
The total farm value of broiler production in the South is about $4 billion — surpassing all other crops as the top ranking agricultural commodity. The broiler industry employs approximately 56,000 production workers in the South and contracts with an estimated 20,500 farmers who “grow out” the birds. Commerical broilers are the region’s biggest consumers of finished feed — an estimated 16.5 million tons. About five million acres of corn and soybeans will go to chicken feed in 1983.
In 1982 broilers were the number one agricultural commodity in Arkansas, Georgia, and Alabama. In North Carolina broilers are second only to tobacco. In these four states alone, the industry turned out 1.9 billion broilers with a farm value of $1.6 billion in 1982.
It took less than two decades for commerical broilers to infiltrate the South. In 1950 small flocks of chickens were kept on nine out of 10 farms in the nation. The South was poultry deficient then, so chickens and eggs were shipped in from other areas. But not for long. By the mid-1960s, the chicken business had evolved from a sideline on the family farm to a giant Southern-based agribusiness.
Why the South? The region’s mild climate provides year-round growing conditions and cheaper fuel bills for heating the houses where broilers are raised. “You also need a lot of small farmers to feed the birds, and a lack of other industry,” explains Paul Alexander of Valmac Industries, an Arkansas and Texas-based company that is the nation’s seventh largest chicken producer. Broiler companies usually locate in rural areas where they can “lock in” their labor force, observes William Heffernan, a rural sociologist at the University of Missouri. “Marginal farming areas in the Southeast provide a work force which can be most easily exploited,” he says.
An Integrated Business
After several decades of fierce competition, a handful of major corporations dominate today’s $12 billion broiler industry. A continuous pattern of overproduction and industry pricecutting has allowed only the largest and most diversified companies to survive in a market flooded with low-priced broilers. Small independent companies are dropping like flies. In 1960 there were 286 federally inspected broiler firms in the United States; by 1981 there were only 137. In 1982 industry analysts reported that 21 broiler firms were for sale — and eight mergers and acquisitions were recorded the same year.
Today the top 10 companies produce 51 percent of all U.S. broilers (see chart). They include diversified multinational corporations like Continental Grain and Central Soya (two of the world’s largest grain companies), and Memphis-based Federal Company, one of the South’s 50 largest corporations. In 1982 C-P Company, Ltd., became the nation’s largest broiler corporation when a subsidiary of London-based Imperial Foods merged with a division of ConAgra. The company slaughters an average of 8.9 million broilers every week.
Chicken giants also include several “independent” corporations which are based almost entirely on poultry products. Gold-Kist is a farm co-op which ranks number 230 on the Fortune 500. Perdue Farms and Tyson Foods are personal poultry empires built and controlled by company chairmen Frank Perdue and Don Tyson.
The major broiler companies are commonly referred to as “integrators.” These companies typically control all phases of producing broilers, processing the meat, and distributing the product. The farmers who raise the chickens work under contract to the integrator. Most companies own their own breeder flocks, hatcheries, feed mills, processing plants, and delivery trucks. Some corporations, like Perdue and Federal Company (Holly Farms) now sell directly to consumers in their own fast-food, fried chicken restaurants. The broiler industry boasts that it is “unmatched for efficiency in all of agriculture.” The statistics are impressive:
• Annual production of commercial broilers has increased from 631 million birds in 1950 to more than 4.1 billion in 1982. Gross farm value has jumped from $533 million in 1950 to $4.5 billion in 1981.
• Chicken is one of the best bargains around — and Americans are eating it up. The price per pound has increased by only 54 percent in the past quarter-century - compared to 195 percent for beef and 188 percent for pork. In real terms, broilers cost less than half of what they did 25 years ago. The average American ate nearly 50 pounds of chicken in 1982, compared to only 23.3 pounds in 1960.
Super Chicken
Without a doubt, the broiler industry’s outstanding performance is due to its ability to breed a “better” bird and, as Successful Farming magazine puts it, its “obsession with wringing every last gram of efficiency out of their product.”
Taxpayer-supported agricultural research at the nation’s land-grant universities is responsible for new technology and rapid growth in the broiler industry. In 1981, for example, land-grant universities in 13 Southern states spent a total of $14.5 million for 312 poultry research projects.
The research runs the gamut; most projects are concerned with the effects on the birds and on production of various antibiotics, growth promoters, other food additives, light, environment, and so forth. Some are general: Mississippi State University, for example, has a project to “study the effects of light and environment on production of broiler chickens.” Some are much more specialized: University of Florida scientists seek to discover whether geese will eat water hyacinths. Some are down-to-earth and practical: the University of Georgia is studying whether running fans at night will improve growth and feed conversion of broilers. The same Georgia researchers are also determining “the effectiveness of microwave radiation for brooding poultry.”
Decades of such research have produced genetic manipulation on a grand scale, and the modern-day, mass-produced broiler bears little resemblance to its barnyard predecessor. A ton of chicken feed now produces 37 percent greater weight gain than in 1955. The average broiler grows from 40 grams to 2,000 grams (a 50-fold increase) in just seven weeks — less than half the time it took to grow a broiler 25 years ago. “If humans grew at the same rate,” boasts a U.S. Department of Agriculture brochure, “an eight-week-old baby would weigh 394 pounds.”
Today’s commercial broilers are uniformly bred for rapid growth, extra-meaty breasts, and for stress resistance to withstand crowded, factory-feedlot conditions. Chickens are raised in flocks of 10,000 to 20,000 birds in a house the length of a football field and one-fourth the width. These growing conditions are the pride of the broiler industry and the scourge of the “animal rights” movement.
Recent studies indicate that the old-timey taste of chicken has been sacrificed to accommodate the commercial broilers’ factory-farm environment. The massive size of a genetically uniform flock of baby chicks requires that they receive heavy doses of drugs for disease resistance and growth promotion. These drugs can alter the taste of chicken. Fifty percent of all antibiotics produced in the United States now go to animal feeds — and the poultry industry consumes a hefty share.
Unfortunately, feed additives can do more than affect the flavor of chicken meat. Antibiotics in animal feed are now considered potentially hazardous to human health. A growing number of human diseases are developing resistance to antibiotics. Studies indicate that one factor responsible for this is the routine use of antibiotics in animal feed, which is passed through the feed to the chickens and ultimately to the human consumer. Exposure to these low levels of antibiotics allows human diseases to develop resistance to the drugs.
Approximately 80 million broilers are mass-produced every week. Despite the uniformity of today’s commercial broilers, the advertising arm of the industry has successfully fabricated “unique” features for each company’s product. The chicken on your grocer’s shelf has been “branded” by the broiler industry. Over 40 percent of all broilers are now marketed under brand names, with distinctive labels like “Cookin’ Good,” “Gold ’N Plump,” and “Young & Tender.” The industry spends $25 million a year on advertising to promote its product – which is rapidly becoming a processed one. “Ice-packs [whole carcass broilers] are going out with the horse and buggy,” predicts one industry spokesman, “There is more profit in a processed item.”
When companies “further process” a chicken, they put the bird in some new form — chicken franks, breaded chicken patties, chicken fillets, and so forth — and then sell it for more than they could get for plain chicken. The extra cost is the result of adding new ingredients, labor, packaging, advertising (to teach you to prefer the processed version), and higher profit margins for the companies. At least 20 percent of the industry’s products end up in fast-food and restaurant chains. Tyson Foods, a leader in processed chicken, already manufactures 450 poultry-related items.
Down on the Factory Farm
In the broiler industry, the chicken farmer is commonly referred to as a “grower.” There is no such thing as an independent family farmer in the chicken business. Ninety-nine percent of the nation’s broilers are produced under contract. If a farmer wants to raise commercial broilers, he or she has to have a contract.
How does the contract agreement work? The farmer provides all the labor, land, and equipment necessary to raise the birds — and agrees to relinquish all major decision-making responsibility to the integrator. A new, fully automated chicken house costs from $60,000 to $80,000. A typical broiler farm has a capacity of 30,000 or more birds, and the grower usually receives four to six flocks a year. Farms with sales of more than 100,000 birds account for 82 percent of all broilers sold.
The integrator provides the baby chicks, feed, and medication. The company delivers the day-old chicks to the farm and picks them up seven or eight weeks later when they are three-and- a-half-pound birds. The chickens are rounded up and packed into cages by the company “chicken catchers.” They are transported on company trucks and weighed on company scales.
The farmer’s work is evaluated on the basis of how many birds in each flock are condemned (because of bruises or disease), and how much feed is used to grow each bird (feed conversion ratio). Since feed accounts for 75 percent of the cost of raising chickens, the objective is to grow a big bird with as little feed as possible.
Most growers have limited contact with the companies they work for. The company “serviceman” is the link between the farmer and the integrator. He or she visits the farm to monitor the grower’s performance and tells the grower when to turn on fans, medicate the birds, or fumigate the houses. The serviceman also determines if and when the grower will get a new flock of chickens. Tom Deans, a grower in Bear Creek, North Carolina, sums up his relationship with the serviceman this way: “The man has total control over me. He has no investment in my operation, but he’s got complete say-so over the future of my farm.”
The vast majority of broiler farms are run on family labor. One of the “incredible achievements” of the industry is that a single individual can manage huge numbers of chickens. Many growers, like most farmers these days, have other jobs in addition to the chicken houses; in many cases, they can’t make it on broilers alone.
Broiler contracts vary somewhat because of weather and growing conditions, but virtually all of them have the same objective. There is no guarantee that a farmer will receive another flock of chickens beyond any seven-to-eight- week grow-out period. For the farmer, it is an enormous investment with no security. “Any mistake you make — you pay for it,” remarks Fitima Groce, a Silk Hope, North Carolina, grower who has raised chickens for 12 years. “It all works to their advantage. Everything falls right back on the grower.”
The contract system allows agribusiness to treat the farmers as employees — without any obligation to pay them as employees or provide them with job security. As long as the farmers are under contract, they are considered “independent” operators. The company thus has no obligation to provide health insurance, workers’ compensation, paid vacation, and so on. And the industry wants to keep it that way. As a result of a recent anti-discrimination suit against ConAgra (the nation’s largest producer/processor of broilers), the industry is now considering adoption of a “model” contract that aims to protect the industry by clarifying grower status. Harold Ford, president of the Southeastern Poultry & Egg Association, explains the industry’s objective: “The farmer is an independent businessman, and should not be considered an employee of the company. This needs to be put in writing.”
Hard Times
According to George B. Watts, president of the National Broiler Council, “The broiler industry has sustained during the early ’80s one of its most prolonged and severe economic downturns.” Even so, industry giants are not really suffering. Federal Company, Central Soya, Tyson, ConAgra, and others have reported increased earnings over the past two quarters. But chicken farmers are feeling the squeeze.
When broiler production is stable, the grower can normally expect four to six flocks of chickens every year. But during a period of overproduction the farmer is expendable. The integra¬ tor controls surplus production by giving the grower fewer flocks of birds — or by simply dropping the contract.
Statistics on the number of growers who have been forced out of business are not available. But there are other signs of hard times. Huge numbers of abandoned chicken houses have be¬ come a striking feature of the Southern landscape. Not all of them are old or outdated. Before making a loan to a new poultry grower, the Farmers Home Administration now requires that county loan officers consider “the number of farms in the area that have vacant facilities ... or do not have a contract due to surplus production.”
A 1983 budget prepared by North Carolina State University indicates that a broiler farmer with a new $62,500 chicken house and 5.5 flocks per year (100,617 birds) can expect to lose money. Nevertheless, major agricultural lending institutions are still making loans for the construction of
new chicken houses. Herbert Gaines, a North Carolina-based Production Credit Association agent, describes what can happen when his office makes a loan for new facilities: “When the integrator decides to go with a new grower, he’s probably going to cut someone else off. That other man who is being cut might also be one of our borrowers. It’s a very difficult situation.”
It is unusual for broiler growers to be free of debt. In addition to the mortgage on their chicken houses, growers are often required to install new, updated equipment at their own expense.
“I bet you that 90 percent of the people who are growing chickens would get out of the business if they could get out of debt,” insists former chicken farmer Devoy Lindley. “You’re just like a dog. You follow the crumbs along, and you get poorer every day — they don’t want you to get out of debt.”
The Lindley family raised chickens for 40 years until they lost their contract in 1982. Lindley recalls, “I had to put in new fans that cost me $1,600. But the very next month they [the company] cut me off — and I never even turned on those fans. The fieldman [serviceman] came out and told me no more chickens. I was shocked. I thought I would be the last one it would happen to.”
Broiler growers are held hostage to a system of corporate peonage. For many, there are few alternatives. Unlike contract vegetable growers, the broiler farmer does not have the option of growing a different crop. Empty chicken houses are not easily adapted to alternative production. Even conversion to turkey barns requires a huge investment and another contract. In some areas of the South, it is nearly impossible to sell a poultry farm.
“How can you sell a chicken farm? Who wants it?” asks Mary Clouse, the wife of a Chatham County, North Carolina, chicken farmer. “Especially when the banks are making loans for new ones. It keeps the farmer on his knees. We’re stuck with it — what else can we do?”
Growers’ Organizing Efforts
“What we need is a poultrymen’s union — where we could all get together and demand more security — but doing that would be just like putting your head on the chopping block,” says one broiler grower.
Under the thumb of corporate integrators, chicken farmers have limited opportunity to organize for fair contracts, increased pay, and job security. Milton Thomas, president of the National Farmers Union chapter in Arkansas, laments, “We’ve been fighting the situation for a number of years. We’ve had special meetings [with poultry growers] but we haven’t made any headway because the growers are not able to do anything. They’re trapped. If they could grow birds independently, there just wouldn’t be a market for their broilers. It’s pretty much the same all over the South — they just don’t have any control over their situation.”
Nevertheless, organized groups of struggling chicken farmers are emerging throughout the South, attempting to gain a voice for growers.
Poultry Producers, Inc. (PPI) is a statewide organization of Arkansas chicken farmers which includes some 1,800 growers. PPI’s former president, Pat Spangler, explains the obstacles associated with organizing: “It’s even difficult to get a list of growers’ names from the integrators. They don’t want anyone to know who their growers are. When the integrator finds out you’re trying to organize, they can put on a lot of pressure. The servicemen have a lot of influence — they’re the ones who tell the grower he’s going to get in trouble. The growers are very strongly intimidated. Tyson [Foods] told a lot of their growers they wouldn’t get any more chickens if they joined our organization.”
In 1981, when Valmac (then the largest integrator in Arkansas) required its growers to install new, costly fans, PPI’s members resisted. As a result, Valmac began to cut back on the number of chickens allotted to its growers. But nobody lost his or her contract. Spangler believes that the growers’ efforts did make a difference. “We have them [industry] a little bit worried. They are nicer and more diplomatic when they deal with the growers now — and they haven’t come out with any new equipment requirements. We did enough so that industry knows we’ll be better organized the next time.”
In southern Alabama more than 120 chicken farmers from four counties formed the Wiregrass Poultry Growers Association in 1973. In 1980 Wiregrass Association went on strike against ConAgra, the region’s largest integrator. Growers charged that the company was short-changing them on feed deliveries, requiring excessive changes in equipment, and condemning too many of the growers’ healthy birds.
For almost six weeks, Wiregrass members closed their chicken houses and stopped taking the company’s birds. When ConAgra officials refused to meet with members of the Wiregrass Association, the growers set up roadblocks in front of the company’s plant, feedmill, and hatchery. Picket lines surrounded ConAgra’s facilities. “The company wouldn’t meet with the growers,” recalls Wiregrass member Fred Daughtry, “but the Federal Land Bank and Production Credit Association [agricultural lending agencies] who have millions of dollars invested in this area, started to get pretty nervous. They knew we were serious.”
It was the lending institutions that finally met with ConAgra. The company later agreed to give the farmers a small raise, and the strike was called off. “It wasn’t really what we wanted,” admits Daughtry, “but things aren’t as bad now. The company has let up on us a lot and the servicemen don’t harass us like they used to.”
Wiregrass is less active now, but members are still exploring ways to improve the growers' situation. The organization is now trying to purchase natural gas for its members (to heat their chicken houses) at a cheaper industrial rate.
What Next?
What future for broiler farmers? Despite their growing numbers, organized groups of contract chicken farmers can claim only a small measure of success. But there is potential for change. A 1979 U.S. Department of Agriculture study of future trends in the broiler industry admits that increasing evidence of “producer activism . . . has possible implications for future production structure and the institutions external to it.” The direction taken by organized groups, how¬ ever, and their success in forming a strong and unified voice for contract growers remain to be seen.
As the South’s leading agribusiness, the broiler industry plays a significant role in the region’s economy and the structure of Southern agriculture. The majority of the nation’s small farmers, though rapidly dwindling in number, live in the South. The broiler industry has helped maintain as well as distort this longtime tradition. Vertical integration in the broiler industry has created a new breed of Southern family farmer.
Under the guise of contracting with “independent family farmers,” the corporate integrators have reduced the real status of contract chicken growers to something less than that of company employees. The integrator tells its farmers how to produce chickens, in what quantity, at what times, and for what prices. For the privilege of getting and keeping a contract, growers must relinquish decision-making ability and shoulder major risks of the business — with no job security.
American consumers have traditionally benefited from bountiful supplies of relatively cheap broiler meat. But as the industry becomes increasingly concentrated and a handful of integrators dominate production, will chicken remain a low-budget item? And can broilers continue to be mass-produced in a factory-farm environment without the use of additives which pose potential risk to human health?
Despite the unparalleled efficiency of modern broiler production, the industry’s structure raises serious questions for farmers, consumers, and the very future of American agriculture. As a growing proportion of U.S. crops and livestock are produced by farmers under contract to corporate agribusiness, we all have something to lose.
Tags
Hope Shand
Hope Shand is director of research for the Rural Advancement Fund/National Sharecroppers Fund in Pittsboro, North Carolina. (1983)