COVID-19 pounded Arkansas poultry workers as government and industry looked on
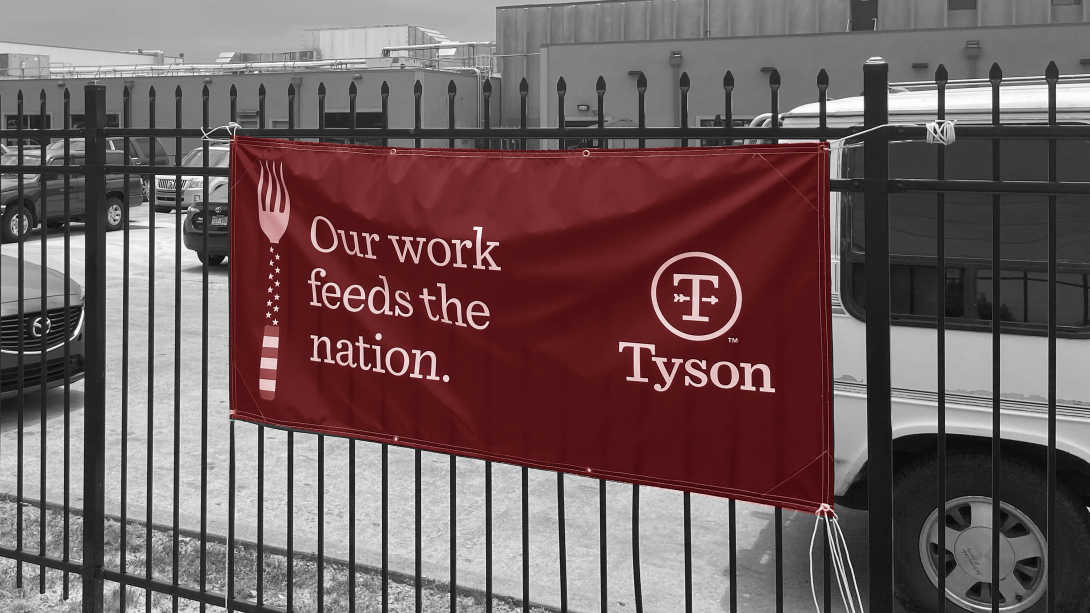
As poultry processing plant workers contracted COVID-19 throughout Arkansas, meat companies doubled down on keeping facilities open — and the chicken supply chain at top capacity. (Photo by Olivia Paschal.)
On June 12, Eldon Alik, the consul general for the Marshall Islands in Springdale, Arkansas, sent an email to mayors, state legislative leaders, and representatives from three major poultry processing companies — Tyson, George's, and Cargill.
"I hope you're all well and healthy!" Alik wrote. "I'm not. I'm not well because my fellow Marshallese citizens are not well and are dying at an alarming rate." His phone had been ringing all week, he continued, with news of Marshallese people who had died of COVID-19. "How many more lives will it take for us to do something? I understand that the poultry plants are essential and that we must continue to open to get the economy going but not at the expense of people's lives."
Marshallese people live in the United States under a Compact of Free Association signed after 67 nuclear test bombs dropped by the U.S. in the mid-20th century contaminated their native Pacific islands with radioactive pollution. In Arkansas, they aren't eligible for Medicare and most aren't eligible for Medicaid, leaving many — especially the elderly— entirely without access to health insurance. Alik estimates that more than half of working-age Marshallese in Arkansas work in poultry plants. Because they often live in multigenerational households, there's a high risk of these essential workers transmitting COVID-19 to uninsured elderly people they live with, many of whom don't regularly see a doctor.
"I wrote that email because I just didn't know what to do, what to say," Alik told Facing South. "I just felt so frustrated." At the virus's peak, he said, more than 600 Marshallese people living in Arkansas were sick. To date, 47 have died. Last week was the first in months that there were no COVID-19 deaths and no funerals to attend.
In his email, Alik suggested that poultry plants shut down for two weeks. That would have given sick or exposed employees time to quarantine and allow for the plants to be deep-cleaned. He wasn't alone: Over the course of the pandemic, many community leaders, workers, and worker advocates pressured industry executives and government officials to shut down Arkansas plants with serious COVID-19 outbreaks.
But that never happened. Two weeks after Alik's email, active COVID-19 cases among poultry workers in Arkansas hit their peak.
* * *
Across Arkansas, at least 35 poultry plants have had five or more workers test positive for the virus, according to data from the state Department of Health. Since mid-May, the number of poultry workers who have tested positive for COVID-19 statewide has increased by more than 4,250%. Currently, more than 4,600 Arkansas poultry plant workers have contracted the virus, more than 1,400 of whom work in Tyson plants. And poultry plant clusters have contributed to outbreaks in many rural Arkansas communities: In Danville, nearly 200 of the 771 people employed by Wayne Farms' processing plant have tested positive for the virus. Pilgrim's Pride and Tyson plants contributed significantly to an outbreak in Sevier County, where more than one-third of COVID-19 cases have been among poultry workers. Statewide, at least 22 workers have died of the virus.
In Washington and Benton counties, the state's second- and third-largest respectively, more than 20% of COVID-19 cases have involved poultry workers — totaling over 1,000 in each county. The poultry workforce in Northwest Arkansas is disproportionately composed of Hispanic and Marshallese immigrants, which has been reflected in the pandemic's toll. According to an early July report by a Centers for Disease Control and Prevention (CDC) field team, nearly half the people with the virus in Benton and Washington counties were Hispanic, and 19% were Marshallese. One-quarter of Marshallese people and 40% of Hispanic people with COVID-19 in those counties were employed in the poultry processing industry.
"We weren't proactive as a state, we were thinking, 'It is not going to be like that here. It is not going to get to us,'" said Maria Romero, a speech therapist in Northwest Arkansas who is on the region's COVID-19 task force. Her mother, who works at a Pilgrim's Pride plant in Sevier County, contracted COVID-19 and was in the ICU for two weeks. She's since returned to work.
When the pandemic began, poultry workers immediately recognized the hazardous conditions of their workplaces — shoulder to shoulder on the processing line, directly facing other workers, little ventilation, few breaks. Some quit altogether, but others couldn't afford to. And missing even a day of work could mean the loss of hazard pay, or marks against their attendance record that could result in disciplinary action.
A former employee of George's Ozark Mountain Poultry in Rogers, a city in Benton County, contacted the city on March 17 asking if the plant would be shut down. He was told by a state health official that the Health Department had no plans to do so. On March 20, workers at two Tyson plants — one in Hope and a second in Pine Bluff — contacted the local Occupational Safety and Health Administration (OSHA) office to complain that management had not implemented coronavirus protocol.
"In the factories, they knew it was there, they should have taken safety precautions right away," Romero said. "They had to see it to believe it."
By the end of May, local fears over poultry plant outbreaks were so severe that Rogers EMS teams were urged to exercise "extreme caution" when responding to calls from poultry plants, according to emails obtained by Facing South. Over Memorial Day Weekend, the Washington County Detention Center, which is one block from a Tyson plant, refused to book Marshallese and Hispanic people who had been arrested into the jail because of the high number of COVID-19 cases coming out of local poultry plants, other emails obtained by Facing South say. The practice was discontinued by Monday morning after some employees raised concerns that it was racist, and possibly illegal. A spokesperson for the sheriff's office told Facing South that one Marshallese detainee was refused, and that the practice was due to a "misunderstanding between day and night shifts" over precautionary intake procedures. "Somehow other agencies were advised we would not be accepting any Hispanic or Marshallese detainees or anybody who works in a poultry plant," the spokesperson said.
At Tyson and George's plants in Springdale, workers affiliated with the workers' justice organization Venceremos gathered more than 100 signatures on a petition demanding plants be shut down and cleaned, which the organization delivered to plant management in May to no avail. Gov. Asa Hutchinson (R), too, continually brushed aside workers' concerns; Venceremos organizers delivered a second letter in mid-July to the governor demanding plant shutdowns. "The poultry processing plants in Arkansas are an essential part of our food supply," Hutchinson said in a statement to Facing South. "It is important for the food service to continue but it is also important for the workplace to be safe. Both our Department of Health and the plants have worked diligently to improve safety."
In mid-June, a local doctor told the Washington County sheriff that his clinic was seeing 10 positive cases a day, "mainly poultry workers or families of poultry workers." But still there was no large-scale response.
As workers fell ill, poultry companies were taking steps to ensure business could continue as usual. In late March, Tyson human resources managers contacted local police departments to ensure poultry plant employees wouldn't be arrested on their way to work in case of a shelter-in-place order. "As the largest U.S. food company, Tyson Foods has been designated by the United States Department of Homeland Security as critical to the infrastructure of the United States," one such email read. Arkansas never instituted a stay-at-home order. And Tyson refused to shutter its plants in the state, claiming such an action would jeopardize the nation's food supply chain.
* * *
Tyson Foods — headquartered in Arkansas's Washington County, with thousands of employees throughout the state — took out a full-page ad in the New York Times, the Washington Post, and the Arkansas Democrat-Gazette at the end of April. It was an open letter from Chairman John Tyson, claiming that the food supply chain was collapsing because meatpacking plants with COVID-19 outbreaks were being forced to close. "Our plants must remain operational," Tyson wrote. "We have a responsibility to feed our country. It is as essential as healthcare.
Tyson has spent well over $1 million lobbying the federal government each year since 2016, and its PAC has contributed hundreds of thousands of dollars to congressional candidates in the last two election cycles. The day after its ad appeared, President Donald Trump signed an executive order declaring meatpacking plants critical infrastructure — an order interpreted by federal agencies to supersede state and local governments' authority to close plants.
One week later, Chairman Tyson spoke to Arkansas' Economic Recovery Task Force, a committee charged with helping Hutchinson plan the state's economic path through the pandemic. According to meeting notes obtained by Facing South, Tyson discussed the "op-ed" — the ad — and said it had "spurred discussion" over the complexity of the supply chain. At the meeting, he told members of the task force that poultry supply chains had been "less impacted than other meat," despite writing the week before in the ad that "as pork, beef and chicken plants are being forced to close, even for short periods of time, millions of pounds of meat will disappear from the supply chain." Tyson spokesperson Derek Burleson told Facing South that the ad was meant to reference "the food supply chain as a whole."
In terms of pure production, it may have been true that the chicken industry was doing just fine. But the industry's processing plant workers, their families, and their communities paid a massive cost for continuing to pump out the nation's chicken. As the virus traveled through plants, it seeded outbreaks outside plant walls and sent essential workers into unpaid quarantine.
"A lot of people did not get paid because they were exposed to it. There was somebody on their line, or they rode the carpools with them to work," said Albious Latior, a Marshallese community leader in Springdale who has been helping to coordinate economic aid to families with breadwinners in unpaid quarantine. Some Marshallese plant workers have missed six weeks of work and pay because they live in households with other workers; when one is exposed, all have to stay home.
Burleson, the Tyson spokesperson, told Facing South in an email that any decision to close plants is "made on a case-by-case basis, involves input from state and/or local health officials and is typically done to enhance health and safety measures, conduct additional deep cleaning and sanitization and/or to conduct facility-wide testing." Tyson did not answer specific questions on whether it had considered closing any of its Arkansas plants.
Poultry companies often didn't tell workers when their colleagues tested positive, didn't pay them for mandatory quarantine days while waiting for test results, and didn't inform them of how to collect short-term disability or other benefits that might have allayed some of the early economic devastation, according to Latior and workers interviewed by Facing South. Many poultry companies that instituted hazard pay for their workers made the pay dependent on attendance, incentivizing workers to show up even when they feared exposure. After the consul general's June email, he told Facing South, some companies began taking steps to compensate Marshallese workers for mandatory quarantine days — but it's often a lengthy process to get those funds, and many Marshallese families don't have much cushion.
"Once they're out of money, they're out of money," Alik said.
Jeff Wood, Tyson's director of state and local government relations who coordinated tours of the company's retrofitted facilities to show off the protective measures taken to stave off the pandemic, wrote a quote praising the cleanliness of Tyson facilities that was attributed to Rogers mayor Greg Hines in a press release announcing that mass testing had detected outbreaks the facilities on the tour. "Sending this quote to you for your review," Wood, Tyson's director of government said in an email to Hines on June 17.
The quote — which appeared in a June 19 press release that showed more than 700 workers had been infected across 10 Tyson facilities in Northwest Arkansas, including 190 workers in Rogers — read in part: "Tyson is not only taking steps to protect the health of their employees, but also helping to ensure the well-being of entire communities, and we are experiencing the benefits of their public service." Hines told Facing South that the quote was "prepared by Tyson representatives" and authorized by him; the Tyson spokesperson said that the quote drew on Hines' "conversations with Tyson representatives, the media, and others," and "captured his words."
"Looks great to me," Hines said in response to Wood's email. Wood replied, "You are great."
* * *
Poultry companies have instituted a slate of safety measures they say should be adequate for protecting their workers from the virus: temperature checks at the door, mandatory masking, plastic dividers between workers on the line.
But outbreaks are still popping up in processing plants across Arkansas. Several poultry plants in Batesville, population about 11,000, have reported outbreaks since July 31. Infections at plants owned by Peco, George's, and Custom Craft Poultry in that town caused the number of poultry workers who had contracted the virus to rise from 12 to 105 people over less than a month in surrounding Independence County. While the number of active cases in Washington and Benton counties have declined in recent weeks, those two counties and Sebastian County, home to two plants with current outbreaks, still lead the state in active poultry cases. Benton and Washington counties have each had more than 1,000 poultry workers contract the virus.
These numbers are almost certainly an undercount, because the current approach to testing in most plants continues to be piecemeal. While Tyson announced in July that they're rolling out testing company-wide, they have not yet announced any results. At plants owned by other companies — Pilgrim's Pride and George's, for example — workers are usually tested by their own doctors when they learn they've been exposed because someone who works near them has caught the virus, or someone else in their household has. They aren't allowed to come into work while waiting on test results, but many companies pay workers for self-quarantine days only if they wind up testing positive.
The lack of testing and the disincentives for regular testing almost certainly mean that there are COVID-19 cases in poultry plants across the state that have gone undiagnosed, people who have been unwittingly exposed, and outbreaks that could have been prevented.
In its mid-June report, the CDC field team found that "prevention, testing, and contact tracing in poultry processing facilities as well as community locations" would be critical in slowing the spread of the virus through Northwest Arkansas's minority communities. After much debate, the Arkansas legislature in July allocated $7 million for contact tracing in the region's Hispanic and Marshallese populations. But there's no similar effort for more rural communities that are being pummeled by the virus's spread.
"I saw a lot of it personally because it affected my family, the differences between assistance, services, and resources in the Southwest, central Arkansas, and Northwest Arkansas area," said Romero, the speech pathologist. "At least someone's getting some help. But how unfortunate is it that if you live in a rural, small town you're just out of it?"
There are ways to make plants safer — but they would likely require increased government oversight, significant investment on the part of poultry companies, and a decrease in production.
"The primary way you make workplaces more safe is just by decreasing the density of humans next to each other. And that's difficult to do" in chicken processing plants, said Steve Striffler, an anthropologist who spent several months working at a Tyson plant in Northwest Arkansas while writing his book "Chicken: The Dangerous Transformation of America's Favorite Food." "The only two things you can do would be completely transform the production line, which would just be massively expensive, or reduce numbers of workers."
One way to distance people from each other in some of the plants' closest quarters is by slowing down processing line speeds. Processing fewer chickens per minute would allow workers to move further apart on the line — from shoulder-to-shoulder, separated by plastic dividers, to the 6-foot distance the CDC recommends for meat and poultry processing plants "if feasible."
ShaRhonda Love, the director of the Arkansas Minority Health Commission, told Facing South that slowing the outbreak will take educating workers about public health guidelines as well as ensuring that "employers are doing their part to make sure they are social distancing those who are working in the poultry plants." A spokesperson for the Arkansas Department of Health said that the department currently "works with employers to help them address their challenges so they can continue [to] operate while following state and federal directives and guidance."
The CDC's guidance says that "changes in production practices may be necessary in order to maintain appropriate distances among workers." But processing fewer chickens is the one thing the industry has always tried to avoid, despite years of health and safety concerns over ever-increasing line speeds. Processing less chicken means making less profit. So far during the pandemic, not a single poultry plant has self-reported to the CDC that they're spacing workers 6 feet apart on the line.
"There's never been any push from the state to do this," said Striffler, "even though we know that's probably the number one thing that would improve the health and safety of workers, regardless of COVID."
Worker advocates have been calling on state and federal agencies to regulate the poultry industry more closely, and create a stronger safety net to make the processing industry a safer place for workers, during and after the pandemic. There are no mandatory federal COVID-19 health standards for meatpacking plants; OSHA has released "guidance," and says it will issue citations only if it determines meat processing companies are not acting in "good faith." A group of food justice organizations filed an administrative complaint with the U.S. Department of Agriculture in July, arguing that the agency's failure to regulate meat processors' line speeds is a civil rights violation.
Slowing the spread and stemming the economic fallout of the pandemic isn't just a question of workplace safety. It means securing economic stability and access to health care for the immigrant workers who make up much of Arkansas's poultry processing workforce.
"If you call them essential workers, that means they're important to the state's economy. But I don't feel they're treated as such," Alik said. "You come to America, you're in this race, and your feet are tied. You can't really run faster. That's why a lot of people are struggling." Access to health insurance and safety net programs for the Marshallese community should also be a top priority for the state, he said.
"This pandemic has really highlighted a lot of gaps, a lot of disparities. And I'm just hoping we don't ignore those," Alik said.
Tags
Olivia Paschal
Olivia Paschal is the archives editor with Facing South and a Ph.D candidate in history at the University of Virginia. She was a staff reporter with Facing South for two years and spearheaded Poultry and Pandemic, Facing South's year-long investigation into conditions for Southern poultry workers during the COVID-19 pandemic. She also led the Institute's project to digitize the Southern Exposure archive.